At Selectaglaze, we have a set way of approaching projects from initial site meetings with clients and architects right through to installation. However, some projects require a different tact – which may include modifying product design to meet requirements, to the way the secondary glazing units are installed. This particular project required a combination of both and has strayed far from the norm of our usual process.
A large office block in an area of London going through major redevelopment was acquired, with plans passed to convert it to residential units. Although not Listed, it was deemed that secondary glazing would be required for two reasons; a cost effective solution to upgrade the windows instead of replacing them all, and to provide the much needed thermal and acoustic insulation to create comfortable habitable units ensuring the well-being of the residents.
The objective was to create a manhattan loft-style living aesthetic, which was not going to be easy given the ‘bog’ standard single glazed metal framed primary glazing.
External view of the building and internal office prior to conversion
As part of the planning and due diligence, an acoustic report was commissioned by the clients, which highlighted that the lowest night time noise levels were, on average, 53dBA. The WHO and NPPF provide guidelines on acceptable levels of noise; with living rooms at 35dB and bedrooms at 30dB. Single glazed primary windows can reduce noise by 30dB and well sealed double glazing by 34dB – so the original windows in this building would not suffice as they were. With the retrofitting of secondary glazing and a cavity of at least 150mm, an acoustic reduction of 45dB+ can be achieved; this proved to be the most desirable solution, as it would also help improve energy efficiency and sustainability of the building. With the windows measuring 1500mm (h) x 4000mm (w) and to ensure the sightlines were matched, the Series 10 3-pane horizontal slider with 6mm low-E glass was specified.
Next to address was how to achieve the intended aesthetics.
Some examples of the stylish dark frames and glazing bars/beading – synonymous with Manhattan Loft Style Living
First, the primary windows were refurbished and painted, so the secondary glazing was powder coated in RAL 7021 black grey to create a seamless look.
The next step was to work out how to create the appearance of glazing bars. After trials in the factory, the final solution was to use a flat aluminium bar fixed to the glass surface with specialist tape, the 2mm x 25mm bar was powder coated to match the secondary glazing. Given that the secondary glazing is bespoke and measured specifically for each opening the glazing bars have to be sized specifically for each pane to ensure a close fit and that slick loft appearance.
The unusual interior design, to maximise the space of the units, sees beds winding into the ceiling and wardrobes fitted tight to the windows. With this in mind, access would be an issue if the installation of the timber sub-frames and aluminium frames were fixed post decoration and furniture install. Therefore, it was decided to install these two elements first and the glazed panes inserted after. Something we don’t generally encourage, but the only way of ensuring a tight and secure fixing to maximise the much needed acoustic and thermal benefits in this particular project.
The showroom was a great success with all the elements coming together – from inside you would never know the transformation that has taken place from an office to chic style loft living; one that is cosy, sustainable and providing peace and quiet from the external environment.
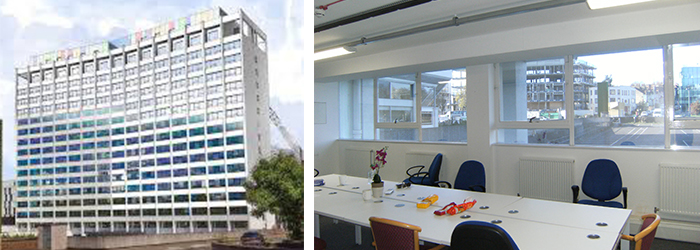
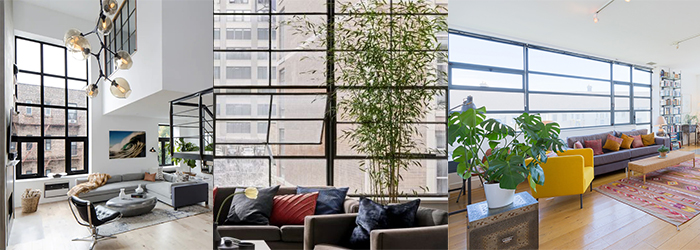
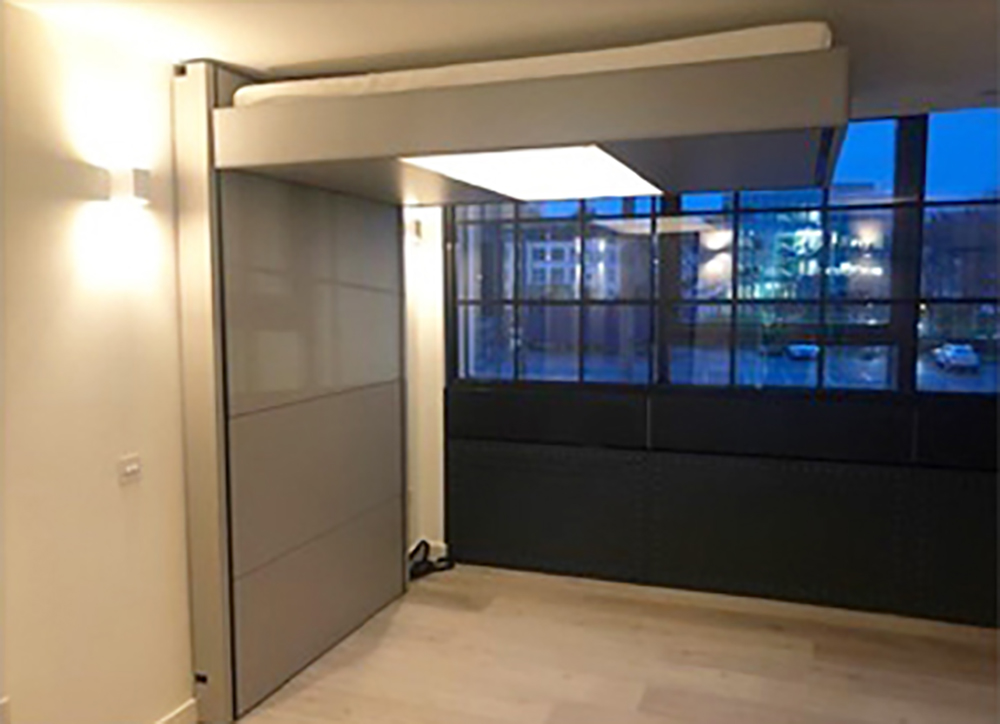
- Date
- Category
- Treat Of The Month